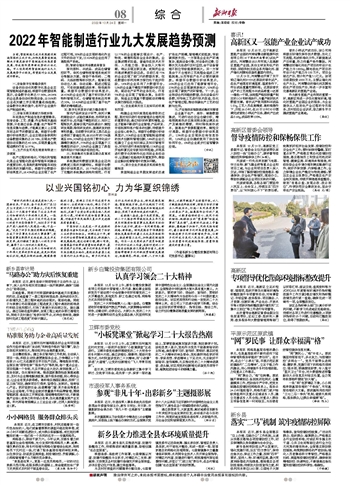
|
当前,智能制造已成为我国建设制造强国的主攻方向,加快发展智能制造解决方案是推动中国制造迈向高质量发展、形成国际竞争新优势的必由之路。市工信局现将智能制造行业九大发展趋势予以转发,希望能对企业发展有所帮助。
一、设备数字化率稳步提升
设备的自动化和数字化是企业实现智能制造的基础,根据平台数据结果显示,设备数字化率达57.98%,24.04%的企业具备自动化物流设备,22.06%的企业在关键工序实现质量在线检测。设备数字化率的提升,有利于企业提升生产制造效率。
二、设备互联互通能力持续加强
车间是生产制造信息的重要载体,包含设备、工艺、质量、作业等相关基础资源,只有通过设备、质量、生产等环节信息采集与追溯,才能真正意义上实现车间各环节的数据互通。根据平台数据分析结果显示,企业实现设备联网和设备数据采集的占28.78%,实现生产数据自动采集的达40.18%,实现质量全流程追溯的仅有16.97%。
三、生产作业可视化程度有待进一步提高
生产过程的标准化、可视化和智能化是企业智能化改造和智能车间建设的重要目标,也是制约影响智能车间投资效果的关键内容。根据平台数据分析结果显示,28.43%的企业实现了生产过程可视,30%的企业实现标准化作业文件的自动下发,10.42%的企业应用了高级排产系统。
四、智能仓储应用场景逐渐普及
面向原料、半成品、成品仓储管控环节,依托仓储物流管理系统或平台等解决方案,借助于条形码、二维码、无线射频等标识技术,能够实现自动出入库、自动运输、配送过程监控,可有效提高配送效率、降低库存量。根据平台数据分析结果显示,28.43%的企业应用了基于标识技术的物料管理方式,仓储管理系统应用率达30%,10.42%的企业实现了基于生产需求的精准配送。
五、数字化研发设计能力稳步提升
面向产品研发设计环节,依托计算机辅助设计、试验仿真系统、协同研发系统或平台,应用基于模型的定义、知识工程等技术,能够实现产品快速设计、缩短研发周期、降低研发成本,提高研发的效率和质量。目前数字化研发工具已在企业得到了普遍应用,由2020年的73%提高至89%,30%的企业应用了数字化设计建模仿真技术,55%的企业实现基于三维模型的设计,32%的企业建立了典型组件和设计知识库并有效应用。
六、系统集成与数据互联仍是高成熟度提升关键点
系统集成和数据互联是企业迈向成熟度三级的关键特征。根据平台数据分析结果显示,20.77%的企业制定了完整的系统集成架构和规范,仅有12.77%的企业能够实现设计、生产、物流、销售和服务全业务的集成。企业集成需求旺盛,普遍存在技术水平低、人员能力弱、资金投入大等问题,难以实现互联互通,或制约企业向高成熟度阶段迈进。目前已有75%的企业实现了部门内的数据共享,但在数据分析利用率方面仍处于起步阶段,14%的企业采用了大数据平台,12%的企业基于模型开展数据分析及应用,驱动生产环节的业务优化,仅有5%的企业实现了智能决策。当前阶段,制造业实现基于数据驱动的精准决策仍面临巨大挑战。
七、企业逐渐关注工业知识的积累和沉淀
构建企业知识库是经验萃取的过程,是对知识进行有效管理并合理利用的重要手段,通过知识的积累和增值,企业才能够不断进行企业管理、产品研发、市场拓展和客户服务的创新,持续提升企业核心竞争力。根据平台数据分析结果显示,31%的企业注重智能制造领域的技术创新和管理创新,14%的企业已经建立了企业知识库以及知识管理平台,对知识进行系统性管理;11%的企业开始积累沉淀专家知识和经验,并将其进行数字化和软件化应用到业务活动中,以期减少经验流失和重复劳作,帮助企业解决经营管理中的复杂问题。
八、部分企业开始逐步实现绿色低碳制造
我国制造企业早期发展追求迅速扩张生产规模,管理模式较粗放,导致碳排放失控。一方面是企业生产环境复杂,能耗设备分散,对设备的过载、空载状况无法进行实时监控,由于设备管理不到位导致能源损耗大。另一方面是由于不合理的工艺流程会造成工序能耗高,从而导致产生不必要的碳排放。根据平台数据分析结果显示,26%的企业已应用了能源管理平台,23%的企业实现碳排放统计,10%的企业实现了碳资产闭环管理。下一步,企业将综合利用能效数据,优化设备运行参数,对传统工艺进行技术改造,优化生产管理过程,推动低碳生产工艺的创新与应用。
九、产业链供应链数据的集成和管理
企业基于生产、库存、销售数据集成,可进行动态安全仓储分析,精准预测库存并实施采购决策以满足生产及销售的需要,同时降低库存成本,提高生产资源配置效率,缩短交付周期。根据平台数据分析结果显示,13%的企业实现供应商信息协同,12%的企业自建或使用了供应商协同平台,6%的企业逐步打造智慧供应链。
(功讯)